As a fan of analog art practices, I decided to learn a new skill to my repertoire. Neon, much like printmaking, is a blend of chemistry, artwork, project planning, engineering, and of course, experimental trial-and-error.
Every single piece of neon signage in the world is hand formed, there are no factories or machinery that can mimic the precision of each turn and bend while keeping true to form and vision due to the restrictions of the chemicals and glass itself. The coloring process and analog planned work in neon sign-making parallels the elements I love in printing, and making tangible artwork. Neon signs have been produced for a short 120 years, so there is not yet any knowledge about the life cycle or expiry of the artwork and lighting itself. I was touched to imagine that in a digital age, printing has a similar unforeseen future of continued existence, and will be readapted – the same way neon signs are seemingly phased out by LED screens of the same purpose, minus the charm that handmade brings – keeping the trend and practices alive.
Every single piece of neon signage in the world is hand formed, there are no factories or machinery that can mimic the precision of each turn and bend while keeping true to form and vision due to the restrictions of the chemicals and glass itself. The coloring process and analog planned work in neon sign-making parallels the elements I love in printing, and making tangible artwork. Neon signs have been produced for a short 120 years, so there is not yet any knowledge about the life cycle or expiry of the artwork and lighting itself. I was touched to imagine that in a digital age, printing has a similar unforeseen future of continued existence, and will be readapted – the same way neon signs are seemingly phased out by LED screens of the same purpose, minus the charm that handmade brings – keeping the trend and practices alive.
All neon signs begin as a glass tube that is heated over a flame, and intuitively bent with restrictions of time and temperature of the glass after it is removed from heat. Due to the nature of glass and the restrictions of neon components and chemicals, each sign varies in how the shapes can be produced with consideration to the rest of the design.
To add the gas and create a power source, I spliced a conductor to each tube of my design by melting the ends of the glass tubes and fusing them together at the right temperature and air pressure. The conductor triggers the neon gas and mercury to become active, having the light shine through as a side effect of the chemical collisions.
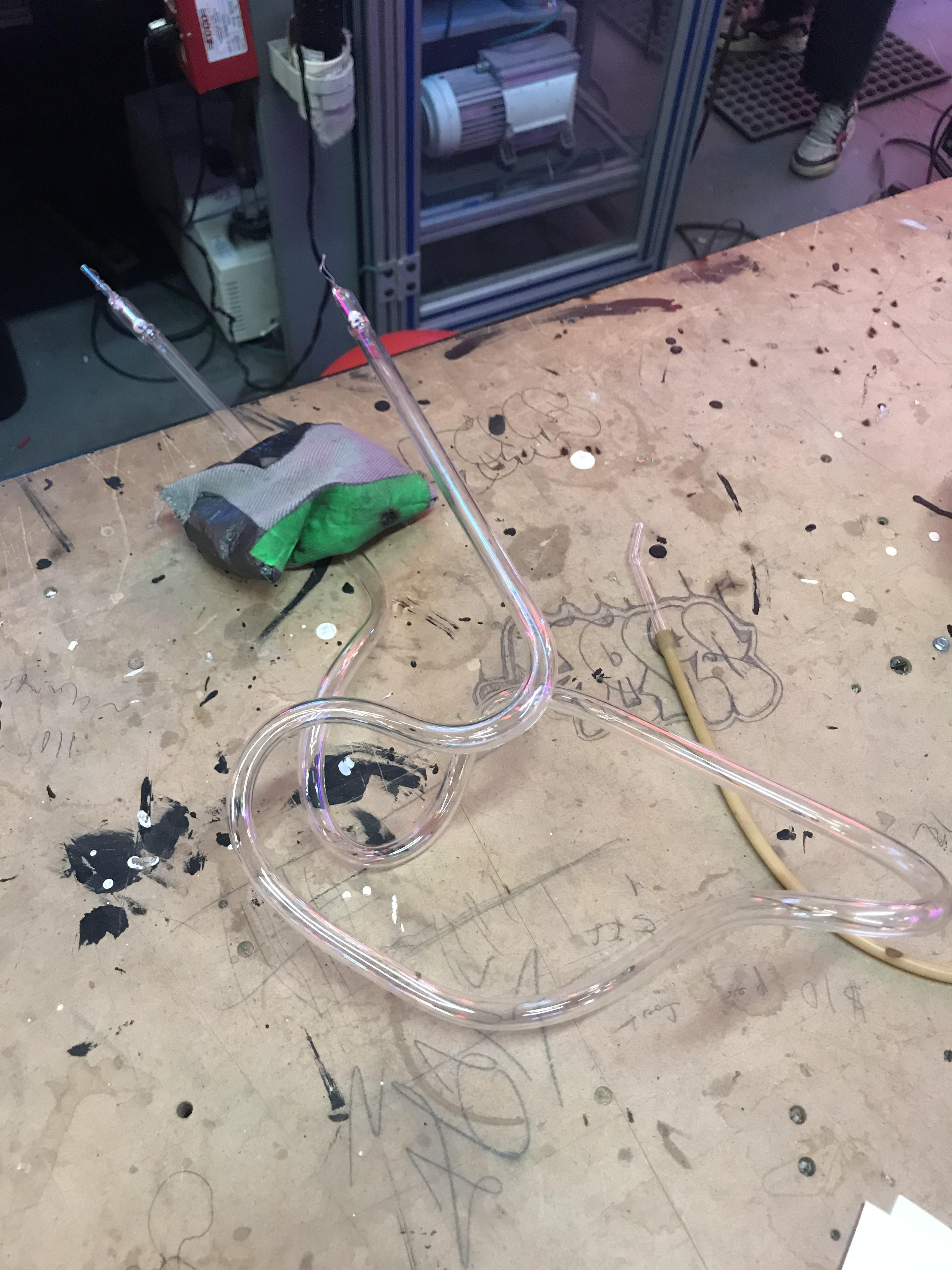
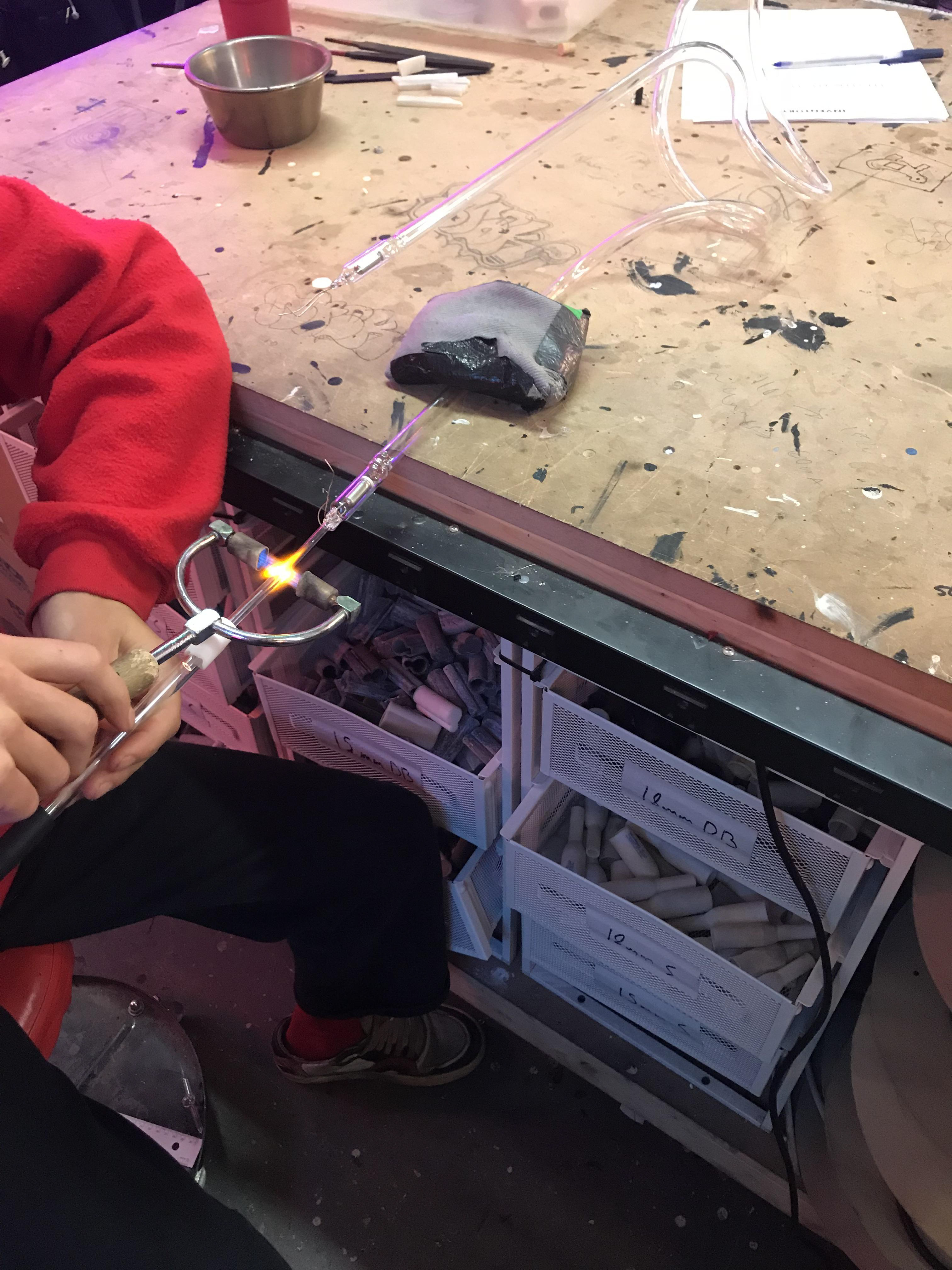
Similar to digital design, neon is colored in a RGB additive color process due to the work centered around emitting light. Each color of what's commonly known as a "neon sign" is designed regarding the shape of the glass as it is formed, the chemicals used to fill the signage, the size of the glass tubing used, and the glass coating (transparent or colored glass). A thinner tube allows for a higher density of color and light due to the air's chemical reactions in a small space. Colors are experimented and color matched in RGB color modes in a balance of gas and glass transparencies. The word "neon" refers to the neon gas that specifically emits a red hue, which I chose for my project to keep the design classic.
FINAL DESIGN:
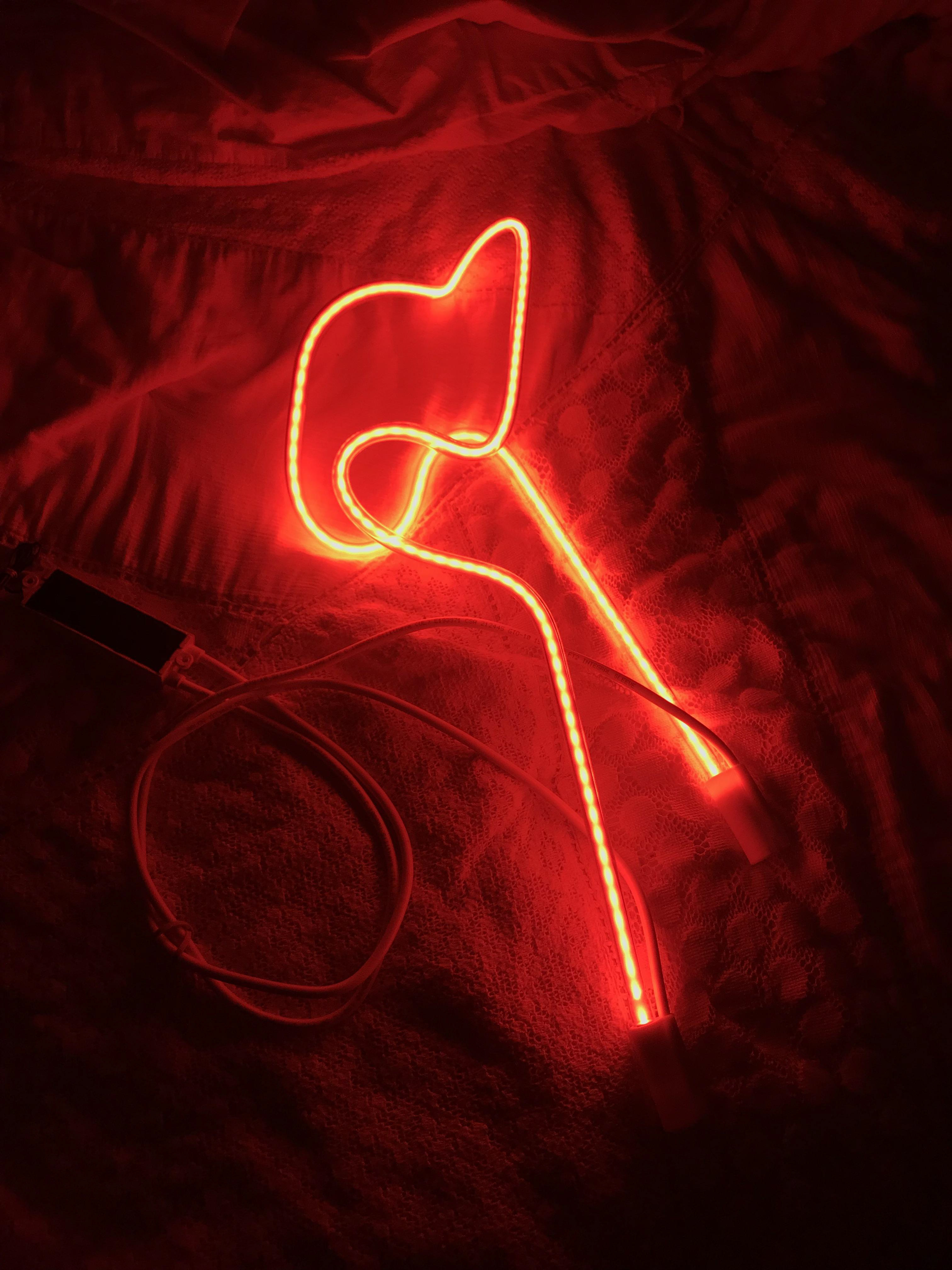
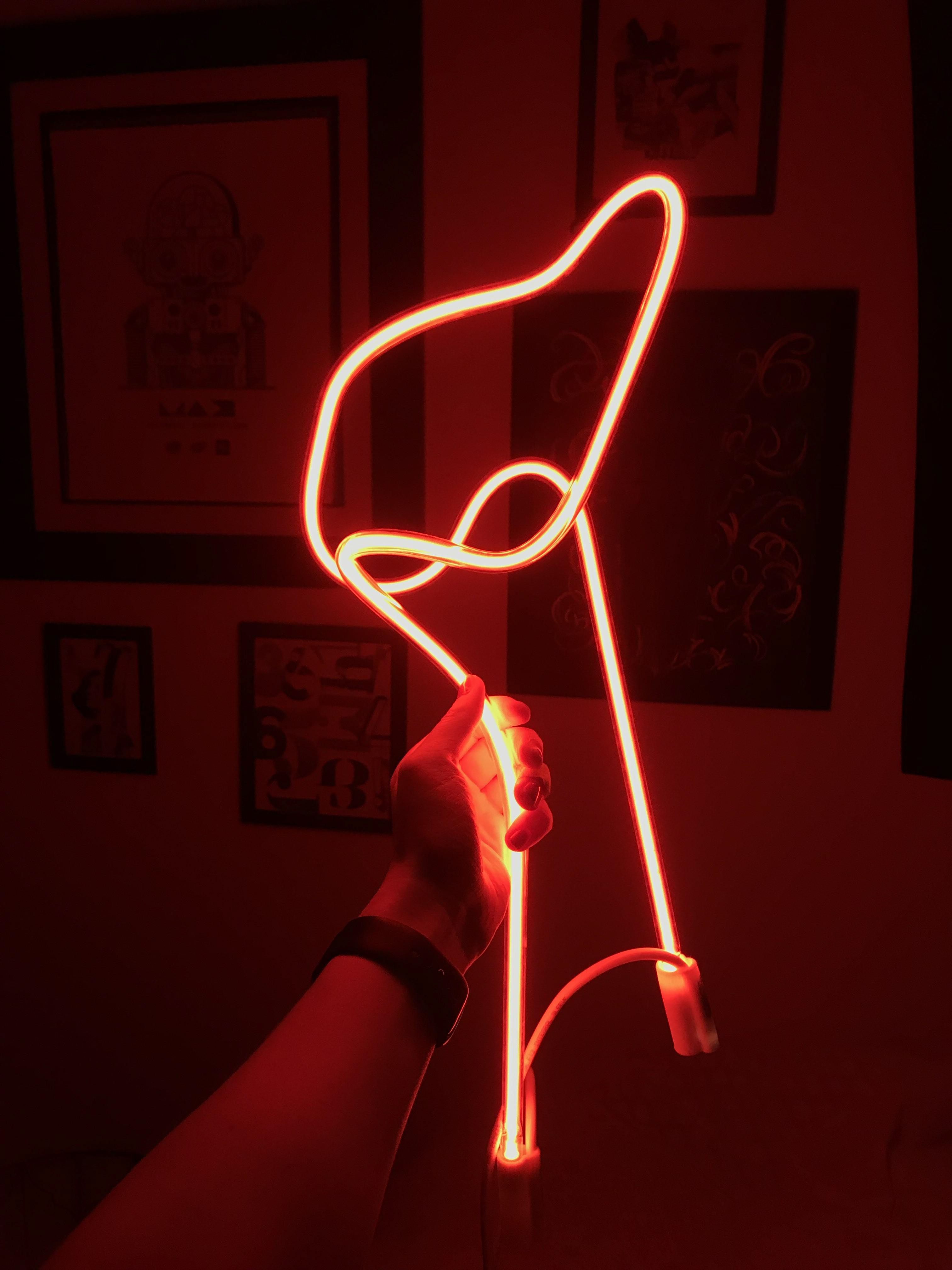
I've titled my final lamp design "Twenty 4" as it took 4 stages of molding the single 4 foot long glass tube to create the design, and I celebrated one of the first few days I'd turned 24 years old by learning a new skill that I can revisit for more projects to come.
TRIAL AND ERROR – LEARNING TO BEND GLASS:
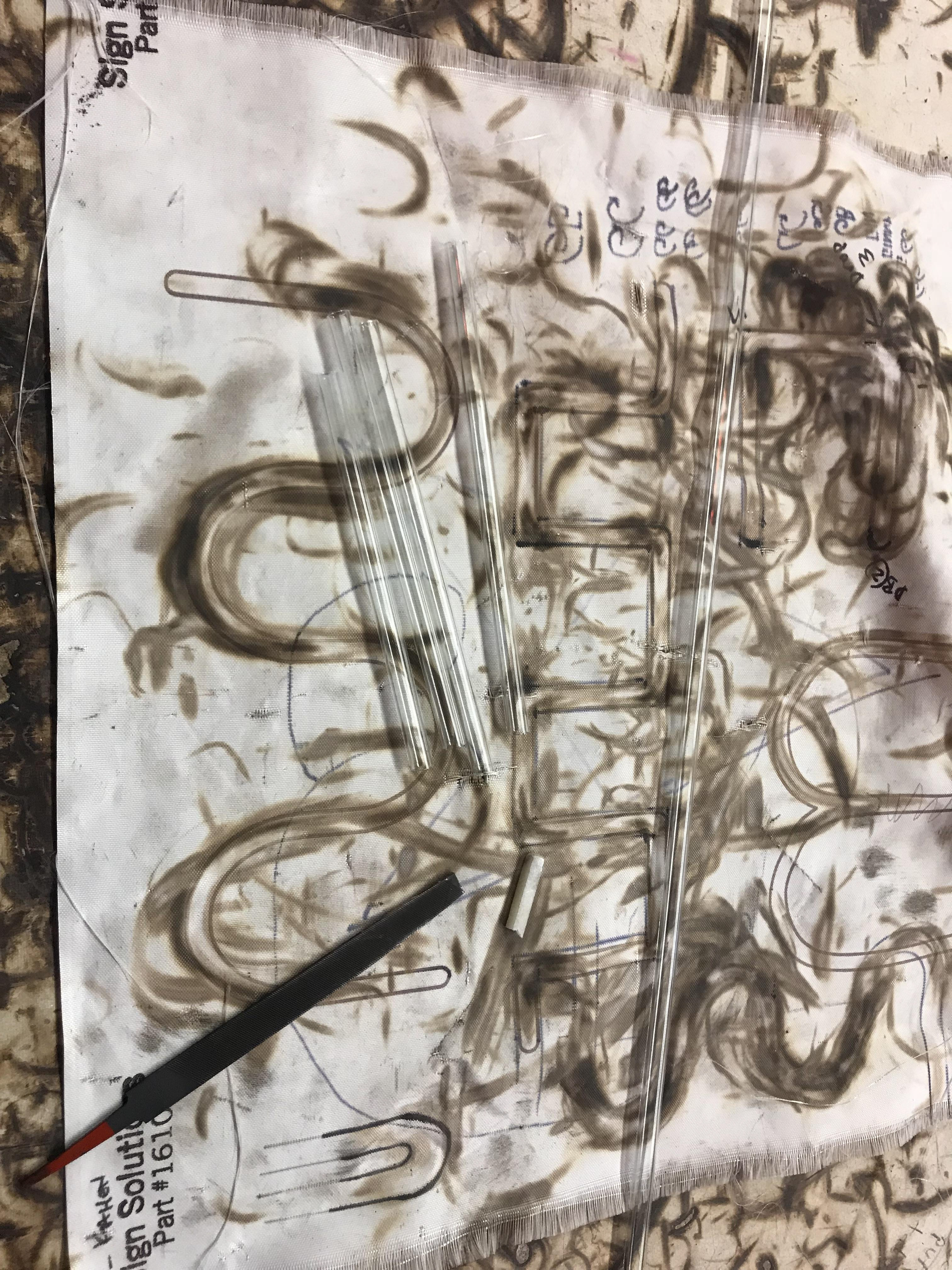
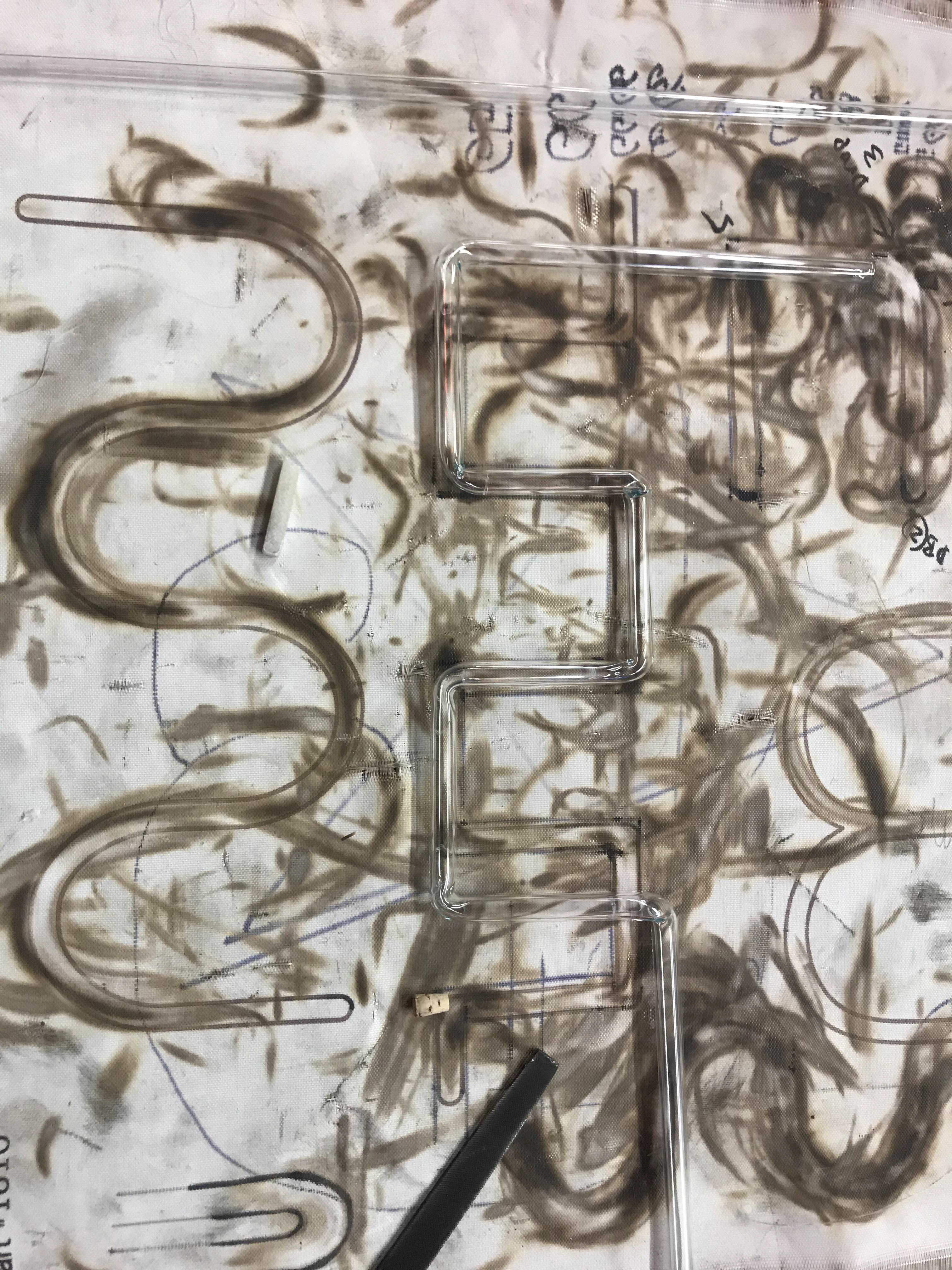
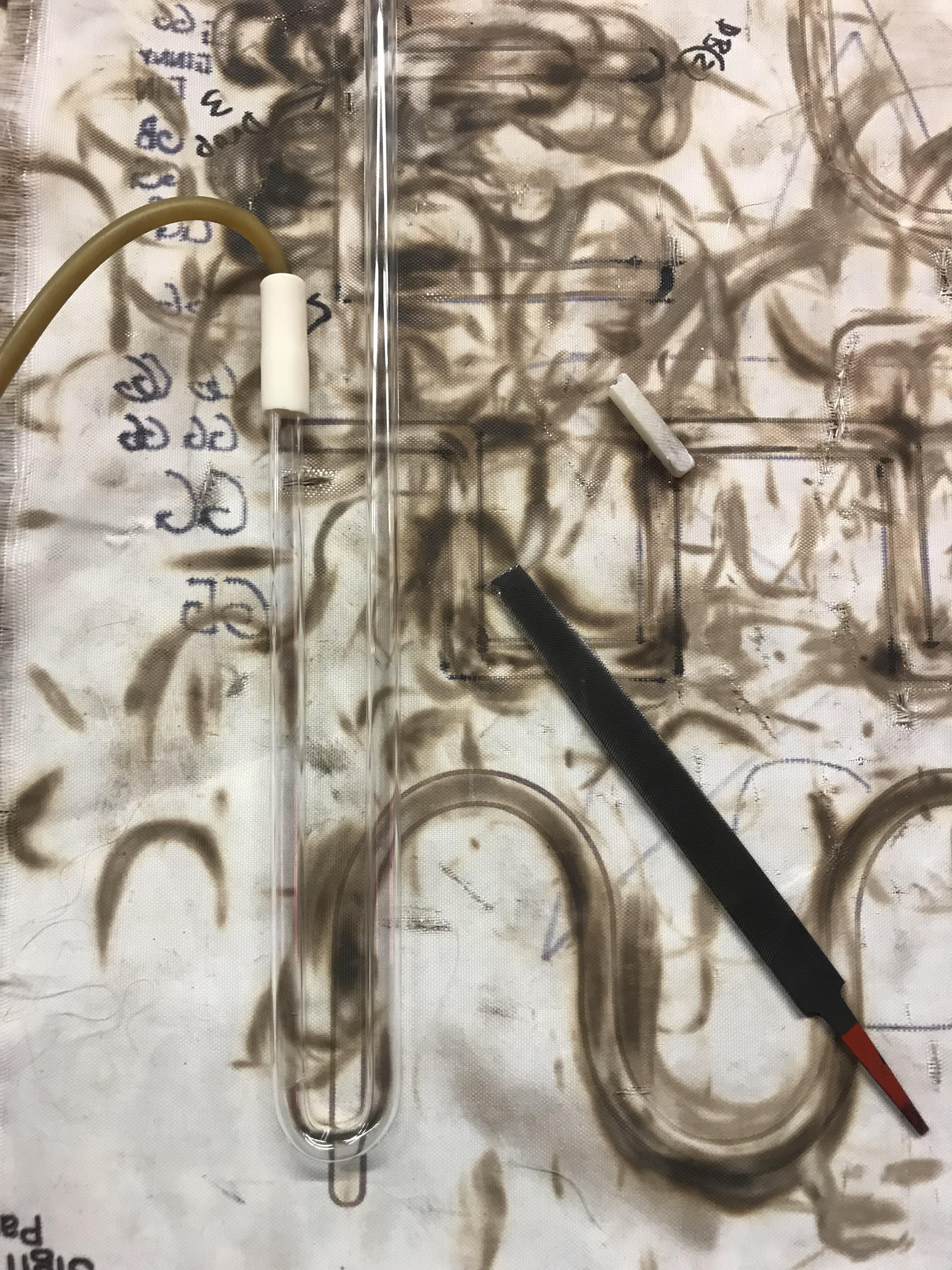
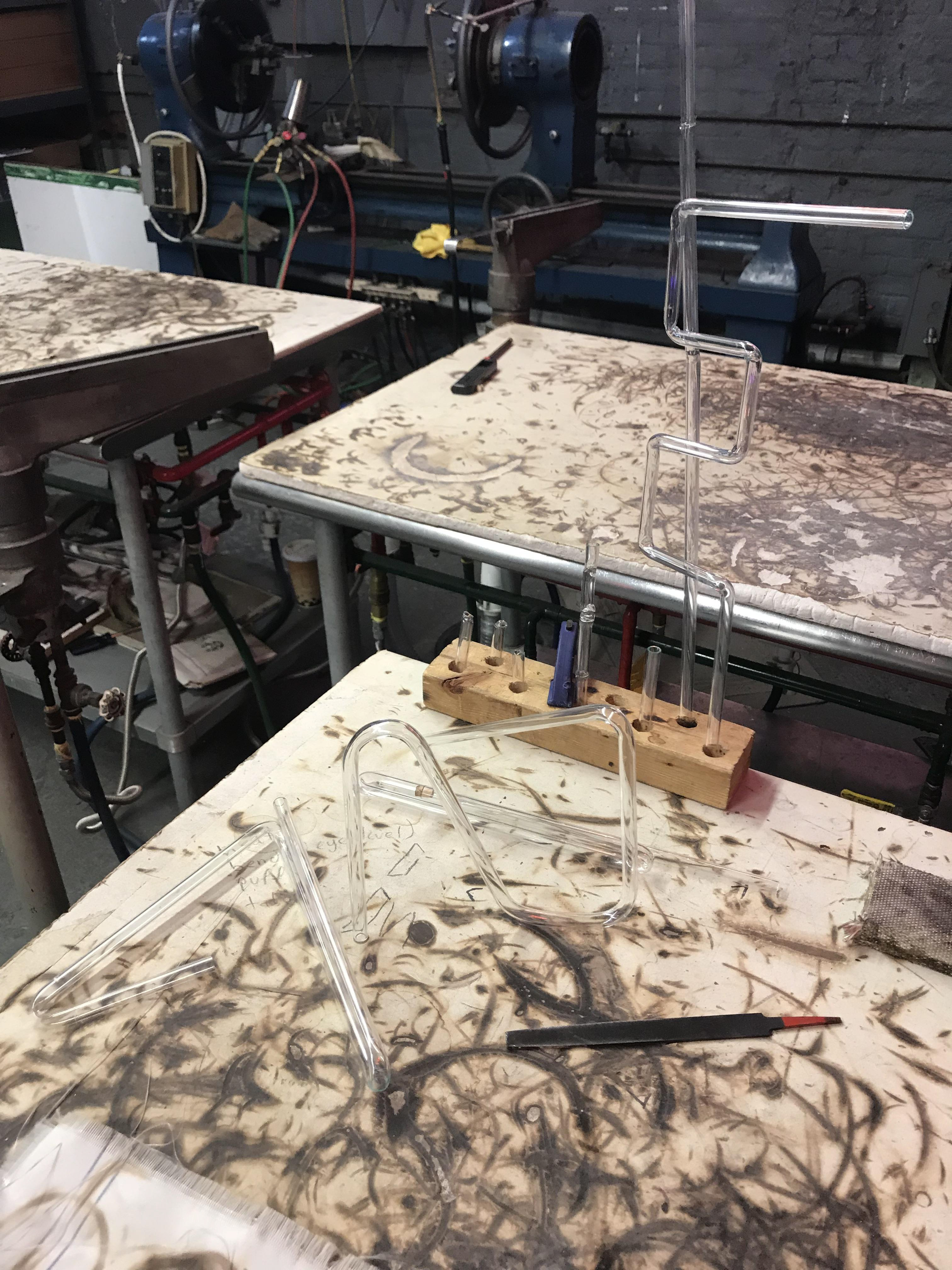